
A Marvel of Engineering
The coil coating process applies coatings and laminates to metal coils in a continuous, automated manner before fabrication. With metal coils up to 72 inches wide and traveling at 700 feet per minute, both sides are cleaned, treated, primed, top-coated, and cured before recoiling for shipment.
Coil coating is known for cost-effectiveness, aesthetics, field performance, and sustainability. It operates as a closed loop system with over 98% VOC capture and conversion to fuel. In the European market, the finished product is referred to as “prepainted” or “precoated” metals or coils.
Click the Image Hotspots to Learn About Our Process
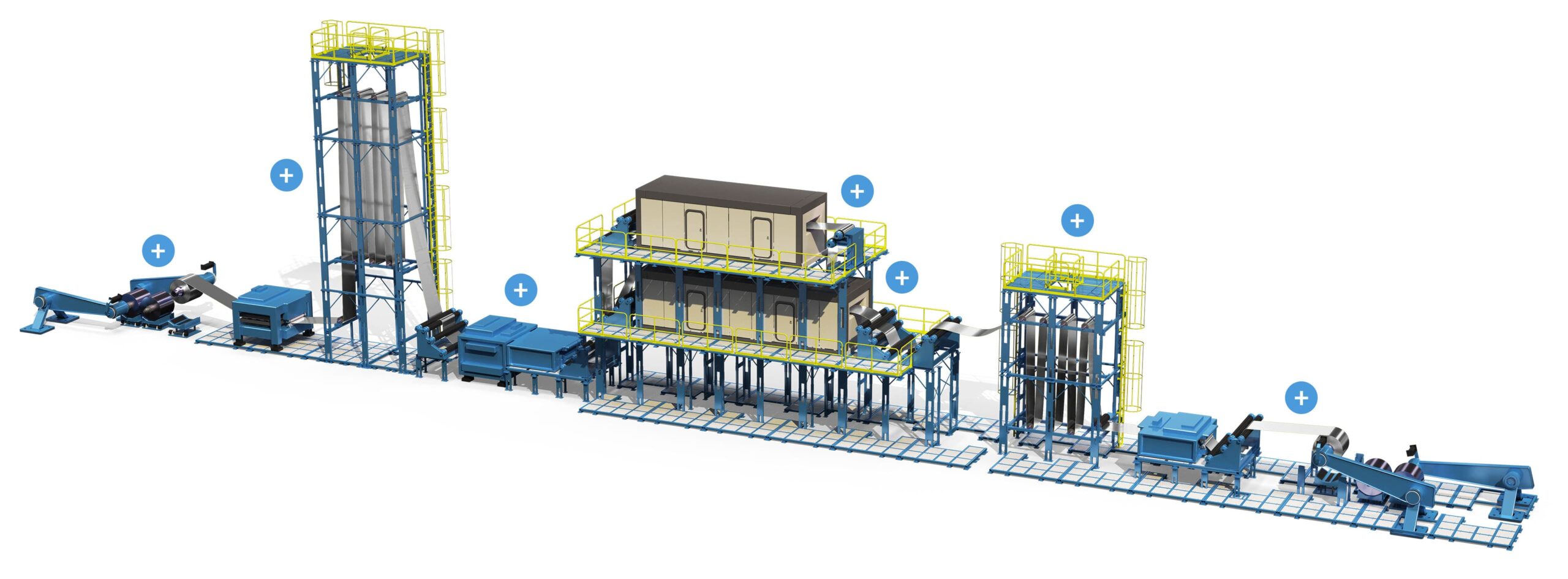
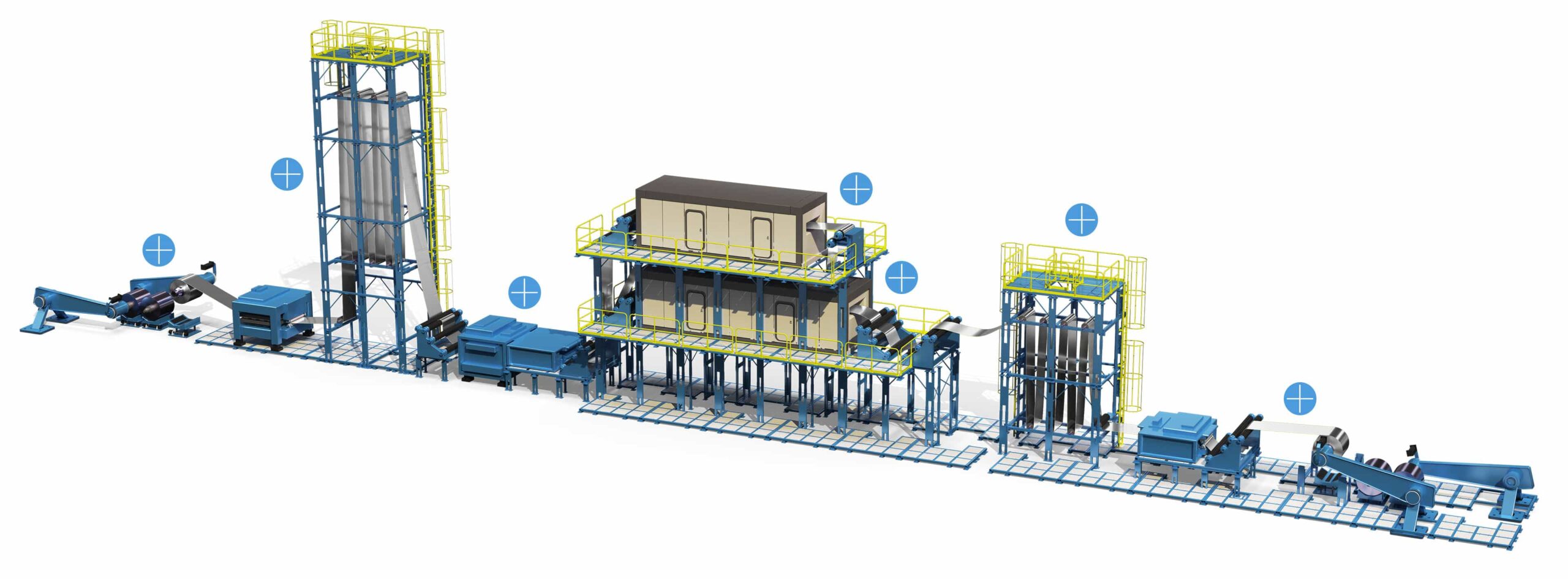
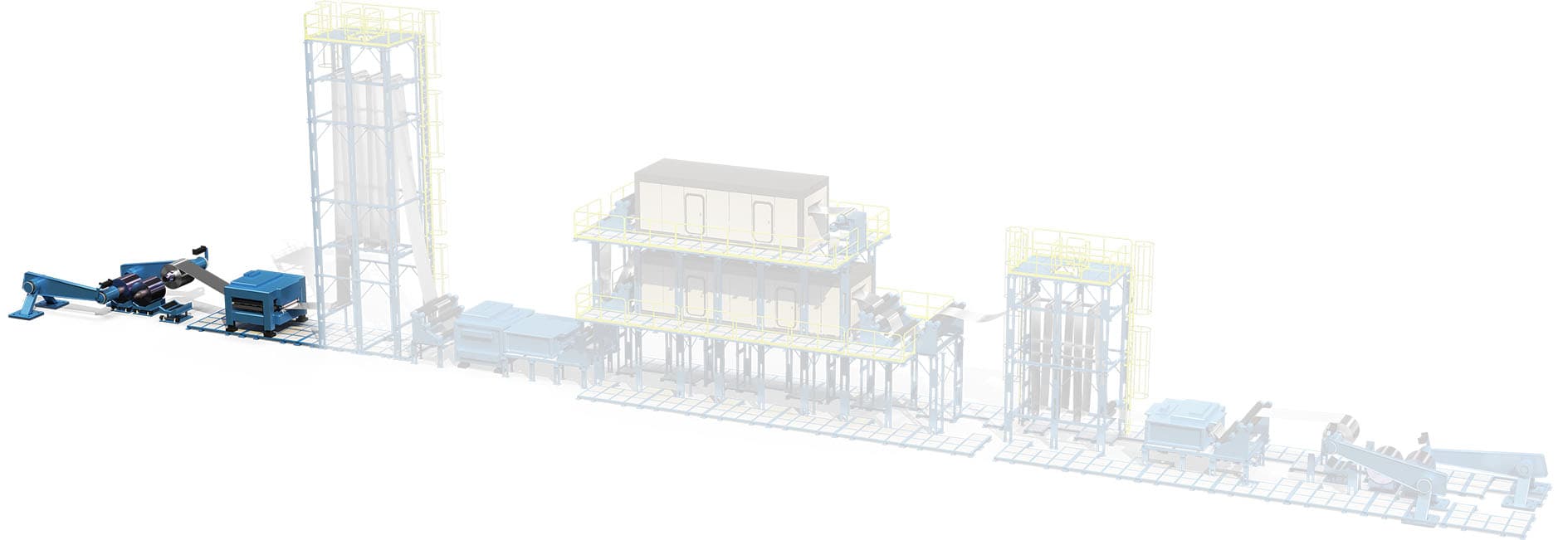
Entry End
Uncoiler
Metal coils, up to 60,000 pounds, are received and undergo visual inspection before moving to the uncoiler for unwinding.
Coil Stitch
At this stage, previous and next coil ends are mechanically joined, ensuring continuous feed in the coil coating line.
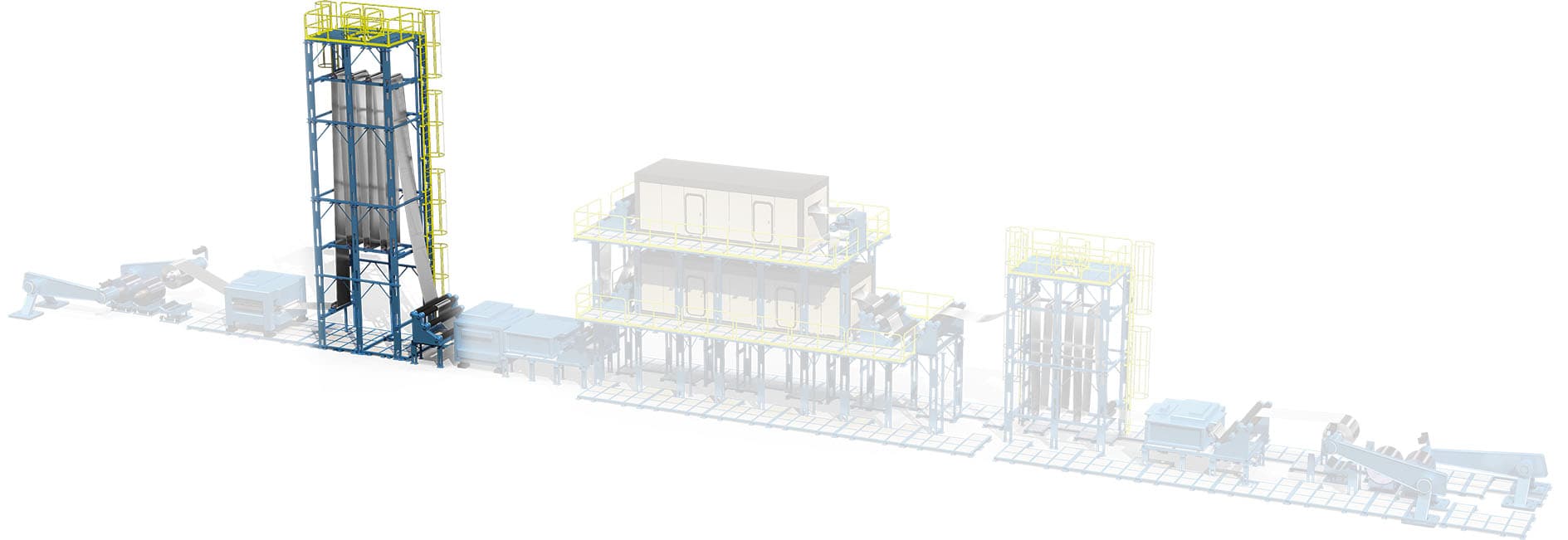
Entry Accumulator
The accumulator is a structure that adjusts up and down to store material, which makes continuous operation of the coil coating process possible. This accumulation will continue to feed the coil coating processes while the entry end has stopped for the stitching process. As much as 750 feet of metal can be collected.
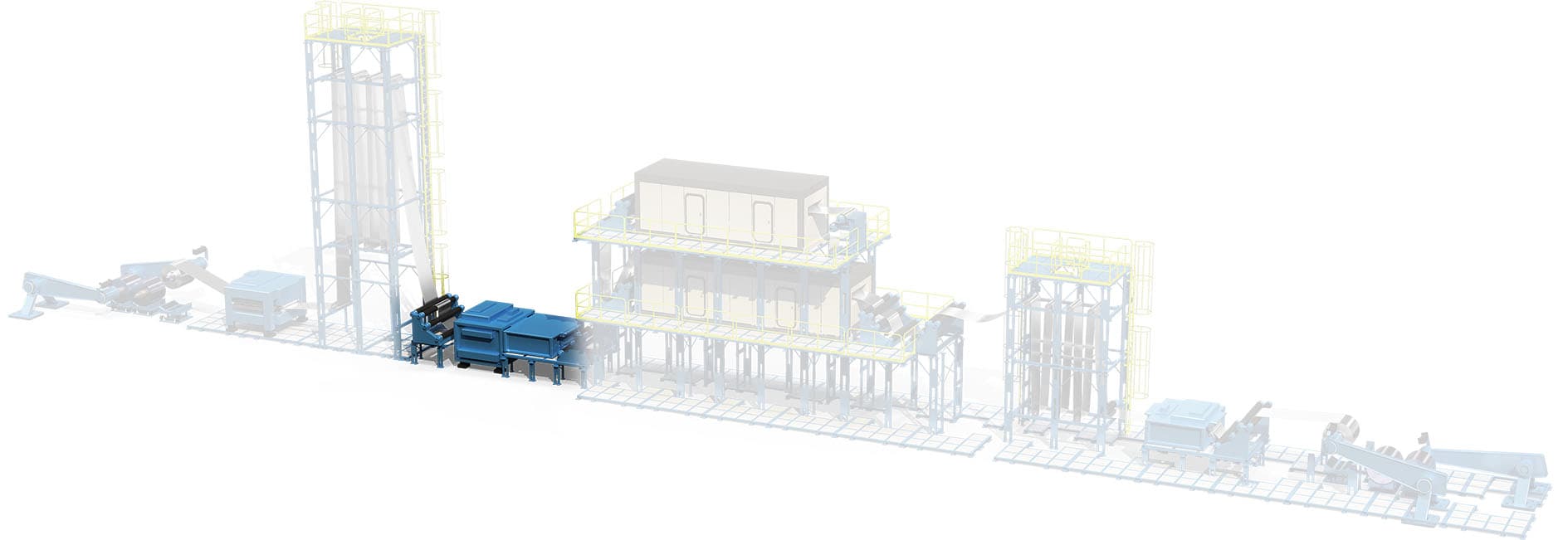
Cleaning & Pretreating
The cleaning and pretreating section of the coil coating process focuses on preparing the metal for painting. During the cleaning stage, dirt, debris, and oils are removed from the metal strip. From there, the metal enters the pretreatment section and/or a chemical coater whereby chemicals are applied to facilitate paint adhesion and enhance corrosion resistance.
Dried-In-Place
In this stage a chemical that provides enhanced corrosion performance is applied. This treatment can be chrome free if required.
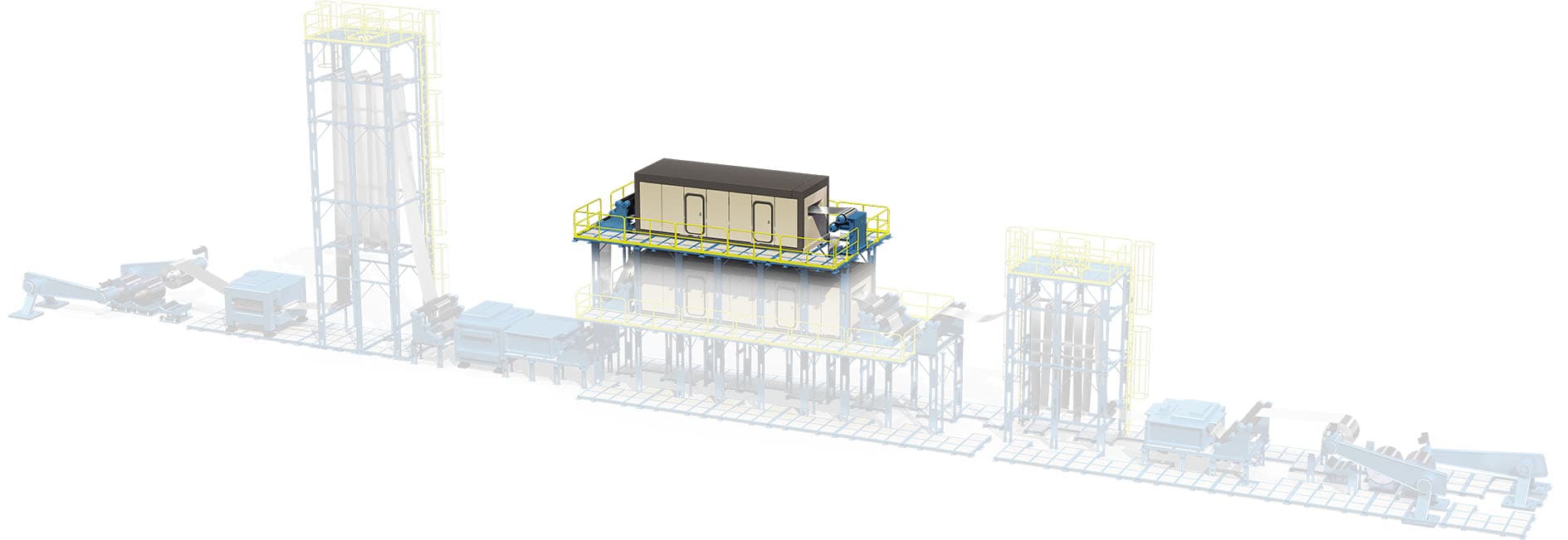
Prime Coat
During this stage, the strip enters the prime coat station whereby a primer is applied to the clean and treated metal. After the primer is applied, the metal strip travels through a thermal oven for curing. Primers are used to aid in paint adhesion, improve corrosion performance and enhance aesthetic and functional attributes of the topcoat.
S Wrap Coater
The S wrap coater design allows for primers and paints to be applied to the top and back side of the metal strip simultaneously in one continuous pass.
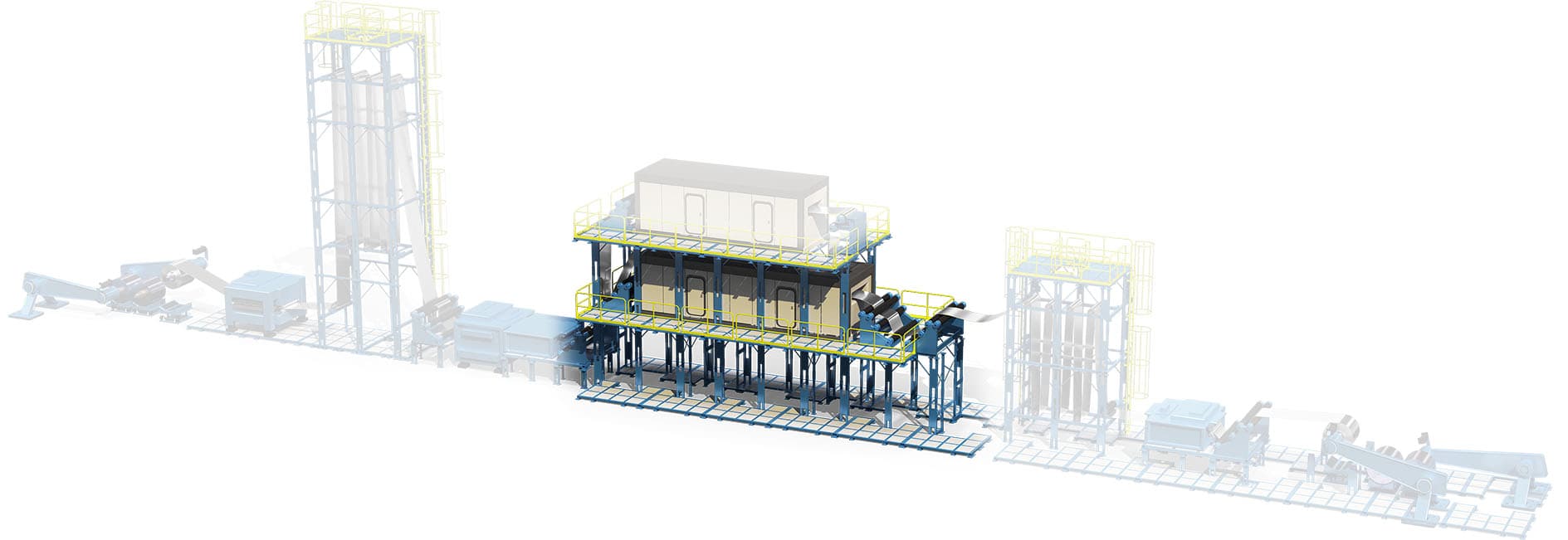
Topcoat
After the primer is applied and cured, then the metal strip enters the finish coat station where a topcoat is applied. Topcoats provide color, corrosion resistance, durability, flexibility and any other required physical properties. Like primers, the topcoat is cured using thermal cure ovens.
Oven
Coil coating ovens can range from 130 feet to 160 feet and will cure the coatings in 13 to 20 seconds.
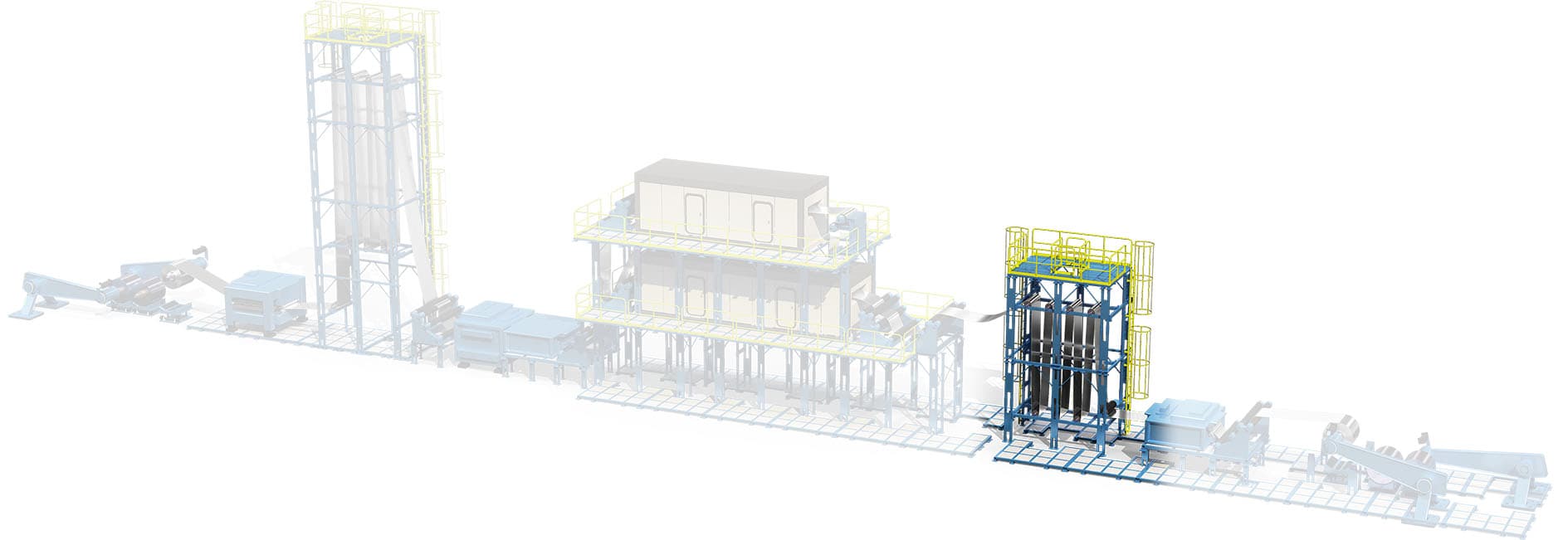
Exit Accumulator
Like the Entry Accumulator, the Exit Accumulator adjusts up and down to store metal while the recoiler is unloading a completed coil.
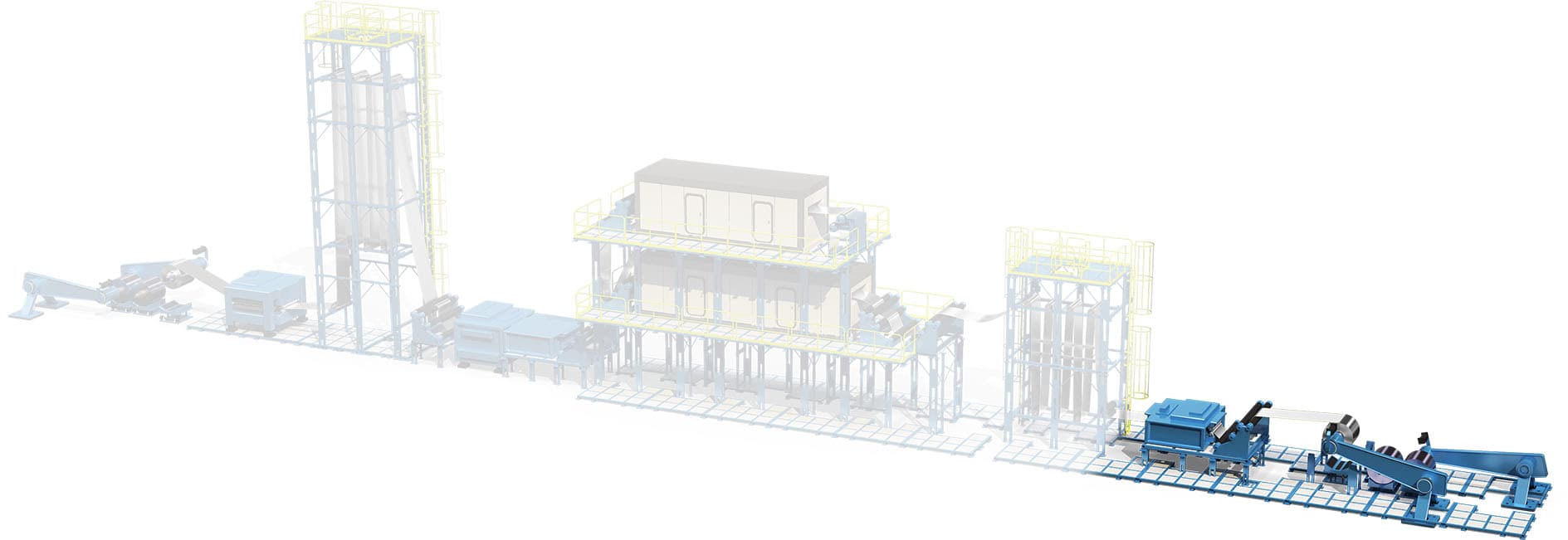
Exit End (Recoiler)
Once the metal is cleaned, treated, and painted, the strip is rewound into a coil size prescribed by the customer. From there, the coil is removed from the line and packaged for shipment or additional processing.